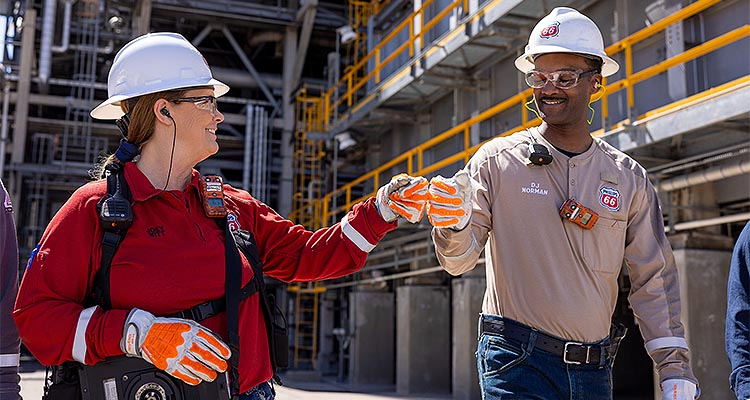
How P66’s Borger Refinery is achieving operational excellence while leading industry transition
As a well-known, multinational energy company specializing in petroleum refining, Phillips 66 (P66) needs no introduction. The Borger Refinery, built in 1926, plays a crucial role in P66’s history. Frank Phillips arrived in Borger shortly after the ‘boom’ began, investing and drilling for oil and natural gas liquids (NGLs). In 1926, he built an NGL processing plant, and a year later in 1927, he bought the existing 1500-barrels-per-day (BPD) Alamo refinery in Borger.
Peak performance
As Phillips Petroleum’s (later to be known as Phillips 66) first refinery, the Borger Refinery has been at the forefront of innovation. In 1930, a much-needed pipeline was constructed between Borger and St Louis, Illinois to carry liquid products to customers in the Midwest. Designed to batch transport different products, this was the first such pipeline in the world, and it was later extended to Chicago, meaning gasoline produced from Texas crude could be purchased by customers more than 1000 miles away.
The first commercial HF alkylation unit began operation at the Borger Refinery in 1942, where the company developed the technology for producing 100 percent octane aviation gasoline. In 1961, the refinery’s first resid cracker was installed to transform residual crude oil into valuable products.
Today, the refinery is owned by WRB Refining, an equal joint venture between P66 and Cenovus Energy, and operated by P66. Its facilities include crude distilling, naphtha reforming, fluid catalytic cracking, alkylation, hydrodesulfurization, and delayed coking units. With high capacities and a clean product yield capability of 91 percent, the refinery produces a high percentage of transportation fuels like gasoline, diesel, and aviation fuels, as well as petrochemical coke, sulfur, natural gas liquids (NGL), and solvents.
P66 assigned a new General Manager, Sean Smith, to the site in 2021. Having started with P66 in 2005, Sean boasts decades of industry experience and expertise, which he has gained from several roles like Refining Process Technology Manager and Manager of Global Optimization. In his current position, Sean is accountable for the execution of projects and long-term performance of the refinery, as well as establishing a strategic plan for the complex with approximately 1300 employees and contractors on site.
“It’s been an interesting few years for all companies across the globe, but we’re seeing the industry recover from post-Covid impact as it returns to a more historical, normal market cycle,” Sean opens. “As an organization, P66 has focused on improving business efficiency through streamlining operating costs, workload reduction, and organizational design. Specifically, at the Borger Refinery, we had to adapt how we operated, transitioning from a mode of minimizing throughput and associated adjustments to maximizing throughput and restoring the work practices previously in place to drive peak performance.
“We recently stopped importing NGLs, going from 100,000 BPD to zero over a multi-year process,” he adds, “which correlates with P66’s decision to build a world-class NGL fractionation and export facility on the US gulf coast. Although we still have work to do to further simplify this area of the complex, we’re continuing to conduct multiple reconfigurations and repurposing equipment, as well as taking equipment or entire processing units out of service.”
Improved processes
In 2023, the Borger Refinery increased capacity by adding and replacing process equipment and optimizing operations. “In doing so, we’ve changed the skyline of the facility over the last couple of years,” Sean elaborates. “We’ve demolished multiple pieces of out-of-service equipment to make way for new construction, including larger crude unit fired heaters, as well as updating and expanding our gas oil hydrodesulfurizer (GOHDS) charge heaters. Additionally, we’ve constructed a new main office building, which has enabled us to consolidate nearly all our salaried staff from 11 buildings into two offices to foster greater collaboration between teams.
“The crude distillation unit has been modified over the years to combine individual processing units into one crude distillation complex. The existing charge heaters were operating at high heat flux rates when the refinery was maximizing crude throughput, which resulted in accelerated fouling of the heater tubes, necessitating unit slowdowns every six months to clean the heater tubes.
“To mitigate this recurring issue, we replaced the three existing fired heaters with two new heaters designed to minimize fouling. These new heaters enable a higher outlet temperature, which increases distillate yield in the atmospheric tower, as well as a higher total crude throughput while being more energy efficient and resulting in lower total emissions.
Meeting consumer demand
“The increased distillate yield recovery in the atmospheric tower lowers utilization in downstream units such as the vacuum distillation unit, coker, and gasoil hydrotreater, which is exploited by increasing total crude rate through the facility,” he elaborates. “The expanded GOHDS charge heaters enable the unit to adjust reactor temperature profiles to improve product yield and quickly adjust to operating changes, all while lowering emissions through the installation of ultra-low NOx burners.”
As the industry continues to evolve in line with market demand for sustainable solutions, the Borger Refinery must make investments to improve production credentials. “We are continuously adapting the gasoline slate at the refinery to align with changing regulatory conditions,” Sean explains. “Our refinery has recently [at time of writing] blended reformulated gasoline for the Denver, Colorado market, for instance, and we can adjust our gasoline qualities to supply specific states that are adopting E15.
“We’re also entering new markets with other ‘boutique’ specifications and continuing to develop and implement projects to adjust our product yields. This will enable us to capture forecasted long-term margin spread between gasoline, jet fuel, and diesel, as well as to provide flexibility to make rapid adjustments to meet prompt consumer demand.”
Community commitment
Amid changing market regulations and as P66’s (heritage Phillips Petroleum) first refinery, the Borger Refinery is genuinely committed to supporting the wider community. The Borger Community Advisory Council, which was revamped in 2021, acts as a pillar of communication between P66, its partners, and the surrounding communities. “P66 and the Borger Refinery focus on four pillars of social impact: education equity, safety and wellbeing, social advancement, and the environment,” Sean confirms. “Specifically, at the Borger Refinery, we support over 50 organizations in the Texas panhandle through annual donations and volunteerism.
“The community recently recognized the need for support in the mental health space – and we responded. P66 was the first to financially support the construction of a dedicated facility and subsequently encouraged others in the community to get involved with supporting the project.
“We’ve also focused on supporting the community in response to the wildfires that devastated the Texas panhandle earlier this year,” he adds. “We had several volunteers fighting fires, and we provided mutual aid and equipment via our refinery emergency response organization as able. We have since coordinated efforts to maximize the ways in which we can support local charities and those impacted by the fires.”
Protecting people and planet
As our conversation ends, Sean reflects on the Borger Refinery’s evolution since he took over as manager in 2021 and suggests how he plans to lead the refinery to further success as the industry continues to evolve. “In 2024, we’re expecting record production levels of transportation fuel, as well as increased market capture,” Sean reveals. “We are continuously focusing on ways to improve the operational availability of the Borger Refinery to better serve our customers and the wider community.
“With this in mind, 2024 will see continued investments across the refinery, although on a much smaller scale than in 2023. Our primary goal for 2024 is to improve operational reliability by resolving longstanding deficiencies in our control systems, addressing end-of-life equipment, and focusing on human performance improvements. Also, as technology is constantly evolving, we have multi-year programs to focus on upgrading our digital controls as older systems become obsolete.
“Further afield, we will continue to focus on production and reliability while implementing improvements to ensure safe and reliable energy for future generations,” Sean concludes. “Above all, we will stay true to our core values of protecting our people and our environment as we strive to be the best neighbors we can be within our community.”
From our conversation with Sean, it is clear to see that the Borger Refinery is embracing change under P66’s careful guidance. With a refreshing perspective and a wealth of industry expertise, Sean is sure to lead the refinery to further success as it transitions to meet evolving demands.
www.phillips66.com/refining/borger-refinery